Motivations and Objectives
The use of structural health monitoring (SHM) serves to assist the monitoring of aircraft structures thus leading to improved life-cycle management and condition-based maintenance. However, monitoring the structural behavior becomes challenging when dealing with operating and environmental uncertainties involved in both vibration-based signals and propagation of guided waves (active sensing SHM), over the variations in the material properties, loads, boundary conditions and so on. In this direction, computational structural mechanics has proven to be a unique tool in the development of numerical models that can precisely capture the operational performance of structures. Physics-based high-fidelity models (HFMs) can accurately simulate the performance of the real system and provide a useful insight while enabling enhanced diagnostic and prognostic methods. While HFMs are the backbone of the engineering design, the computational cost is increasing when simulating large scale, unsteady numerical problems. Along these lines, the demand for multi-fidelity approaches consisting of simplified techniques, able to deliver results in a limited amount of time, is growing rapidly. In this content, surrogate modeling has gained attention, aiming to reduce the computational cost of HFMs while providing results in a limited amount of time towards the realization of the digital twin (DT) concept. Reduced order modeling (ROM), as part of the surrogate modeling, has extensively been applied to decrease the simulation cost, while preserving the dominant effects of the HFM. ROMs have emerged as a useful technique to decrease the computational cost of numerical simulations and provide solutions in a limited amount of time.
Main Contributions
The major aim of this work is the development of a robust and accurate ROM framework, that provides real-time solutions, aiming to assist the SHM systems. A machine-learning (ML)-based ROM mentioned as FastSVD-ML-ROM is developed to reduce the costly and time-consuming experiments while providing real-time physics-based solutions. The FastSVD-ML-ROM is utilized to approximate the high-fidelity solutions, extracted by structural dynamics analysis, using the finite element method. The established ROM is integrated with the stochastic data-driven models to implement a robust DT system. The main applications of the ROM are summarized below:
- Uncertainty quantification to examine the effects of the variation in the material properties
- Accurate damage diagnosis - damage identification and localization
- Speed-up the computationally costly high-fidelity numerical solvers
Method of Approach
The FastSVD-ML-ROM is composed by a combination of machine learning models and linear algebra techniques. In particular,
- A truncated Singular Value Decomposition (SVD) update is employed to calculate the basis vectors of large snapshot matrices during the simulation process.
- To identify a low-dimensional embedding through non-linear dimensionality reduction, Convolutional Autoencoder (CAE) is utilized.
- A Long Short-Term Memory (LSTM) network is applied to predict and forecast the temporal scales of the latent representations in unseen times for a given parameter vector in real time.
- A Feed Forward Neural Network (FFNN) is employed to map the input parameters sets to the first temporal sequence of the LSTM network during the online phase.
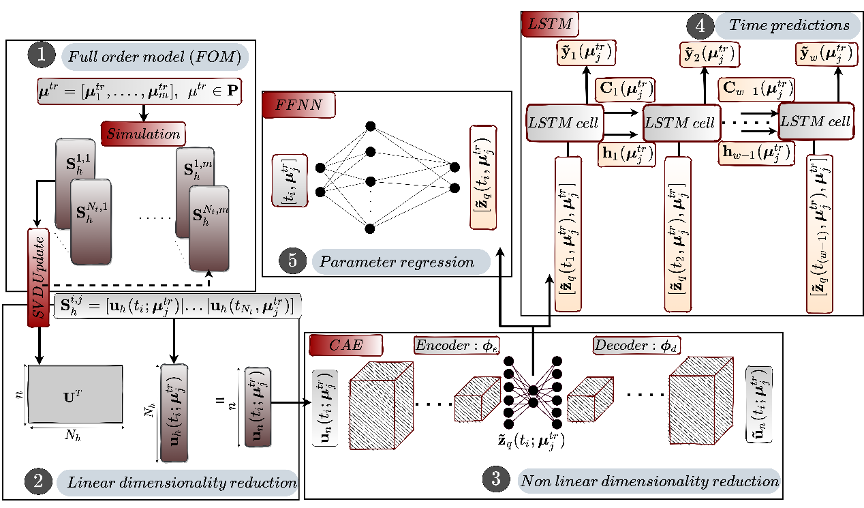
Indicative Results
In this case study, we aim to establish a robust DT system accounting for the UQ introduced in the material properties. The main goal is to set-up an efficient surrogate model able to perform a forward uncertainty quantification (UQ) analysis and examine the effects of the variation in the material properties. To achieve that, HFMs are simulated using the FEM aiming to provide the unsteady acceleration distribution through the uncertainties of the young modulus, the poisson’s ratio, and the density introduced in a light-weight aluminum plate. As a second step, the ROM is trained and tested by the generated numerical data. Finally, the developed ROM is used to replace the HFM and investigate the UQ of the acceleration fields by simulating several cases, while reducing the computational cost several orders of magnitude. of a thin aluminum plate structure with the FastSVD-ML-ROM. We consider the transient plane stress structural problem that simulates the wave propagation on a light-weight aluminum plate. The results of the true and predicted results are presented for the testing parameter μ_te^1=(67.2 GPa,0.33,2695 kg/m^3) at t = 0.000075 s (Fig. 2-top) and μ_te^1=(71.1 GPa, 0.33, 2695 kg/m^3) at t = 0.0001 s (Fig. 2-bottom). We note the ability of the FastSVD-ML-ROM to accurately predict the acceleration distribution on the plate. For μ_te^1 an error e_rmse= 0.06 is obtained (accuracy in mm), while for μ_te^2 the error e_rmse= 0.03 (accuracy in mm). To further access the performance of the FastSVD-ML-ROM, in Fig. 3, we present the evolution of the acceleration a_z on the point a,b,c, and d for the μ_te^2. It is obvious that the FastSVD-ML-ROM can accurately monitor the acceleration values in z-axis near and far from the excitation location and effectively model the time-varying (non)linear dynamics, including complex wave interaction phenomena.
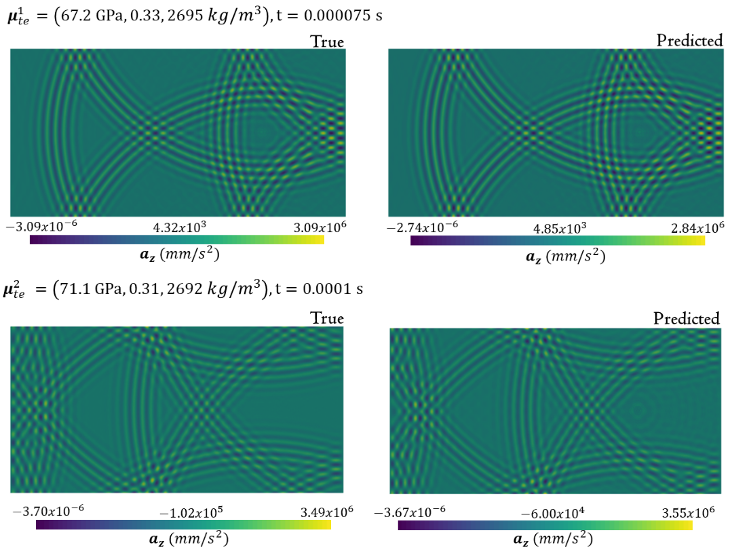
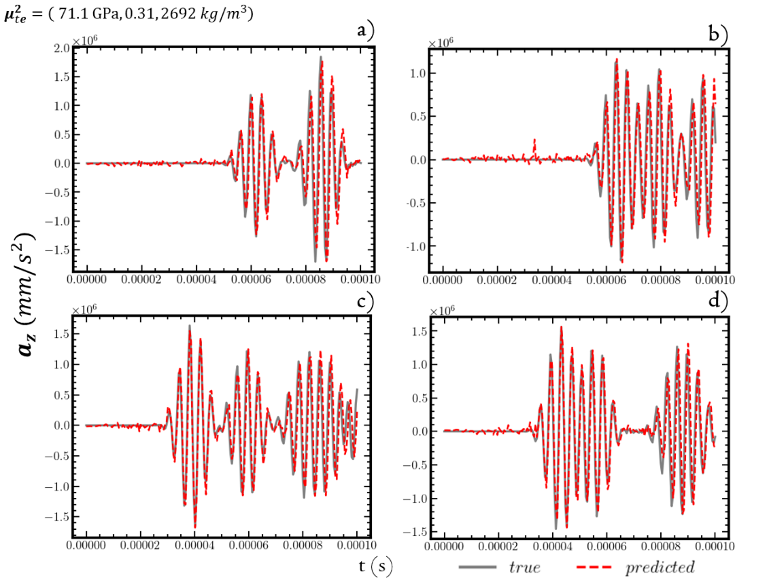
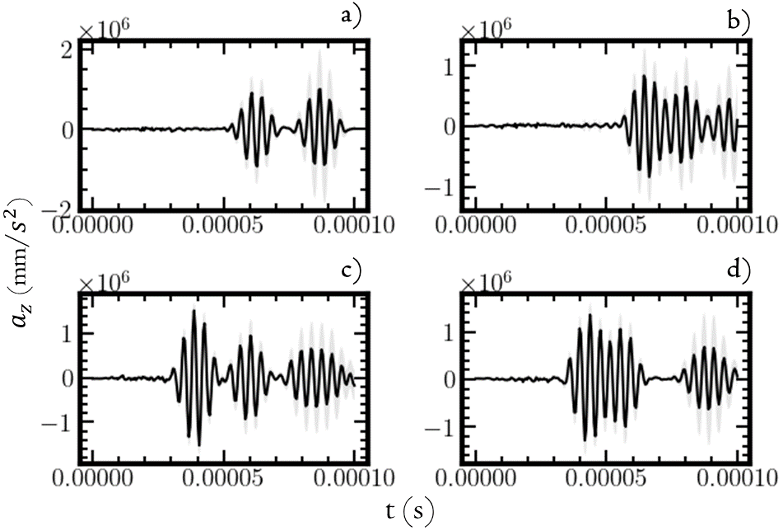